Gaffers Tape Home Depot
Hello Haunters! A Pepper's Ghost is theatrical illusion that was originally developed in the 19th century to make it appear as if real life ghosts were on stage with the actors.
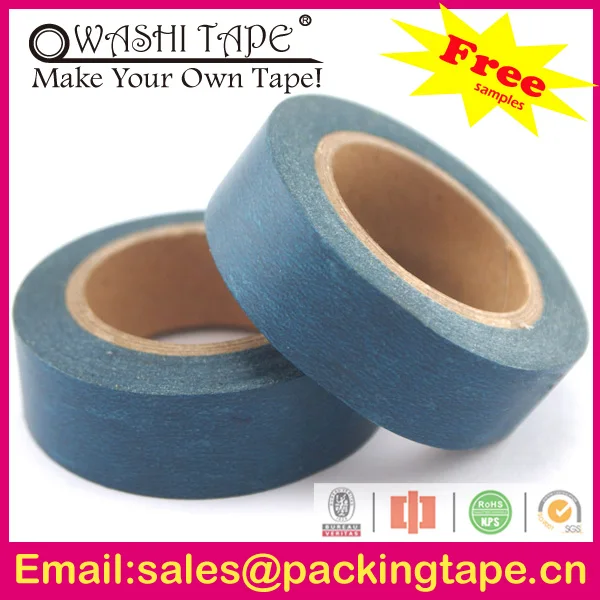
Shop our selection of Black, Gaffers Tape, Tape in the Paint Department at The Home Depot.
It has since been used time and again to delight and intrigue viewers. Most notably is the use of Pepper's Ghosts in the Disney Haunted Mansion ride. In this tutorial, I will show you how to set up a Pepper's Ghost in a rather confined space. Items required: 1 Roll Gaffers Tape 1 C-Stand (I rented mine from a movie production rental house) 1 Projector 1 large mirror 1 piece of Lexan or Plexi Glass larger than your opening (smaller sizes can be purchased from home depot or lowes, but for larger sizes it is cheaper to goto a plastics company) 1 Large piece of white paper 1 Large piece of black cloth 1 Wood Clamp Curtains or Artificial Spider Webs 1 piece of 1X2 8' long (or however tall your piece of plexi is) Accessories Step 1: The Basics. After tons of research on instructables and other sites and even in that long forgotten medium: books, I discovered that there were three basic approaches in how to produce this illusion. Before we look into the options, however, let us first look at the illusion and how it is produced.
In it's most basic sense, the Pepper's Ghost can be broken down into three elements. The first element is the subject. The subject can be many things, but it is what will form the content of your illusion. Whether it is an actor offstage or in this case, a projection, it will ultimately be the focal point of the illusion. The second element is the picture plane. This is the heart of the illusion. The picture plane serves a dual function in that not only does it reflect the image of the out of view subject, but it also is transparent so that the viewer can see the 'set' beyond.
The third and final element is the viewer. Without a viewer, well.this would be a bit of a waste:) There are three basic ways to organize these elements. The Subject being above (which is easiest with a projector), the subject below (most common in theatrical use), or the subject to either side. I chose to use the side since it required the least amount of construction and rigging and seemed to work best for my space.
It is important that you choose the right method for you. Now my first problem was that I knew this was going in my office (I wanted it indoors to protect it from the elements but also to keep sticky curious little fingers off the plexi) but my office is relatively small for this kind of illusion. So my first step was to measure and draw up my office. I am an architect so this is my approach.there are probably many ways, but this is the easiest for me. If you are not in the design field, a good shortcut is to get some graph paper, and assign a measurement to each square. For instance, on the page, every square would be equal to 1 foot.then you can draw a proportionally accurate layout of your space.to scale.
The above line drawing shows my office and the layout for my illusion. Step 2: Standing Up the Plexi. Let me explain the progression of the image and then I will explain the construction.
My theory on how to do this in a confined space was that I needed to bounce the image at least once in order to get the size up to real life size. Sure one could buy a short throw projector, but I actually borrowed the projector and frankly, my wife puts me on an allowance every Halloween and so spending a grand or two on a projector probably isn't going to fly. So If you look at my drawing you can see that the projector shoots the image, which passes through the plexiglass, hits the mirror, passes through the plexi again, and is projected upon the surface of the wall behind the projector.
My projector sat on the ground and was angled up slightly so that there would be no interference. You could also position your projector to the side but then you run the risk of the viewers being able to see 'how the sausage is made' Ok.so now that the theory is done, let's get physical. The first and most important item is the plexiglass. This can be glass as well or as some have talked about, window weather proofing. I actually purchased some of the 3M stuff but couldn't figure out a way to accomplish what I needed to do without building a lot of extra framework.
Glass came to about 7 bucks a square foot at the cheapest, which was expensive, plus I didn't want to run the risk of shattering the huge panel I needed (4' X 8'). When deciding on the size of your panel, remember that getting it to the size of your opening is not enough. Fiskars Telescoping Pruning Stik Manual Transmission more. If you are going to be angling it up or down, it needs to be taller than your opening, or if you are doing it as I did, side to side, then you need to get a panel wider than your opening. My window was 6' tall by 3' wide so I bought a 4' x 8'. Now.assuming you have procured your items, then it's time to get to work. I started by trying to stand the plexiglass up.
Obviously, this was not going to work on its own as a piece this size has a tendency to bow. I took a piece of 1x2 I had left over from another project and ran it through my table saw at a depth of about 1/2' using a 1/4' dado blade. Now this may be greek to a lot of you, but what I did was put a groove the entire length of the piece of the wood 1/2' with a width of 1/4' I then slid the plexiglass into the slot I create and now I had made a frame for one edge of the plexi. I positioned this support piece as close to the window frame as possibly since it will be visible to the ToTs.
I did not, however, try to disguise it as I figured they would be too distracted by the illusion to notice a small stick of wood running the up the edge.I was right. Step 3: Securing the Picture Plane. I secured the wood frame at the top of the window using Gaffers tape.
I cannot recommend this tape enough. It is a tape used in theatre and movie production. It is very strong, very sticky and very reliable. It won't take the paint off and it will hold. Buy it.don't substitute with painters tape or duct tape. Buy the gaffer's tape. So now the Plexi is able to 'stand' on it's own, however, it is not very well supported and it still seems like it is bowing quite a bit.
Plus I think if one of my cat's came in and tapped it, the whole thing might collapse. So here I took a page out of the book of those who came before me and rented a C-Stand. A C-stand is a support armature used in photography which can extend up and out to hold something while staying out of frame. Step 4: Still Securing the Plexi Glass. It was at this point I realized I had no means with which to attach the C-Stand to the plexi-glass. Thankfully my in-laws had just given me some wood clamps for my birthday so I attached the wood clamp to the plexi and then the C-Stand to the wood clamp. I actually 'aimed' high with the C-Stand so that when I attached it, the counter weight would support the heavy plexi-glass and remove a bowing issue I was having.
So now the plexi is supported and stable. It will require fine tuning but that comes later. Step 6: Setting Up the Projector.
Next, we set up our projection system. I used an optima projector I borrowed from a local school. Schools are a great source of projectors because they all have lots of em and rarely use them. Make friends with a teacher or administrator. It's worth it. I placed the projector on the ground. I had to stand it on it's side since my illusion was for a standing figure (Daisy from Spectral Illusions.) If you are doing something horizontal oriented, then you can just keep it flat, but angle it up a little.
If your projector is on the ground, then you have to aim it up slightly. Step 7: Multiple Images Are Bad! In a perfect world, we all have enough room and hardware to create the kind of pepper's ghost that doesn't require shooting through the plexiglass multiple times. However, in a confined space, it becomes necessary to do just this. And as a result, there are secondary reflections that must be dealt with.
I've made some diagrams that I hope will help. Forgive the sloppy nature of them.I did them very quickly. The first image above depicts the path the light travels from projector to the projection surface.
These are two of the three steps the image goes through in order to achieve the illusion.The light leaves the projector and as it leaves, because of the lens, it is expanding in all directions. First, the light comes into contact with the plexiglass. As a result of this contact, some light is reflected. This is inevitable. It is also why you see a small version of the bride projected below the window in the image in the original post.
This is an artifact and is not a good thing. If this shines into the viewers field of vision, it creates bright spots and pretty much ruins the effect.The light that is not reflected continues through the plexiglass and hits the mirror. Now remember, the image is still expanding.The light then bounces off the mirror and heads to the plexiglass again (right side of the drawing). The same thing happens here as happened before, but now, the artifact is being projected backwards. This was why I had to hang the black cloth. To prevent a 12 foot tall bride from being visible at the back of the scene.Once again, the light not reflected travels through the plexi and hits the projection surface behind. Once the light hits an opaque surface, it is done expanding and this is the final image you will be using.
In the second drawing you see how the plexiglass is now being used as a mirror. The light from the projection surface is being REFLECTED in the plexiglass, not TRANSMITTED through as it has been so far. This is why the viewer can see it. It's the same principle as why, on a sunny day you can look around and see the world but the sun is a bit harder to look.
It is the difference between looking at the source of the light or looking at it's reflection. Step 8: We're Done.or Are We? The projector shoots an image onto a large mirror.
Here the Gaffer's tape comes into play again. Love this stuff.and my wife loves that mirror.and my cats love to bat at things.GAFFERS TAPE TO THE RESCUE!! Turn on the projector and aim it at the mirror.
Look behind you to see where the image is hitting on the wall and adjust mirror and projector accordingly until it is at the height and position you would like it to be. If the wall you are projecting onto is flat white, that is great!
However, I grabbed a large piece of paper, about 36' x 96' and gaffer taped it to the wall. This provides a nice soft clean surface which will only help you in the illusion. Now.about this time, if it is dark out, you will wipe your hands, arch your back, smile and think 'AH. This is perfection.' Then you will turn around and notice that there is a giant phantom projection on the wall directly opposite the window. Step 9: Getting Rid of the Phantom.
Well it makes sense. If the plexi is able to shoot an image out the window, of course it is shooting it backwards at the same time. I failed to take a photo of it, and I apologize for that. But on the wall at the back of the room (if you look in the drawing) I hung a large cheap piece of black felt. It was on sale a Michaels I think for like 2 bucks a yard. 3 yards was all I needed. I hung it up high enough to absorb the projected phantom, and then as an added bonus, I laid books on the shelves to create little mini shelves.
I draped the fabric over these and placed artificial candles on them. This was nice because it provided a backdrop for Daisy and emphasized the fact that she was see-through.
Step 10: Tweaking and Setting the Scene. So now, all that's left to do is to carefully tweak everything. Adjust the location and angle of the projector, skootch the mirror this way and that, and most importantly, adjust the plexi. If it is bowing even slightly, your ghost will look weird. It pays to be slightly OCD on these things.
Once the image is perfect, dress your set! Remember, you are creating a play here. This isn't just some static prop with a strobe on it.
This is a scene. This is theatre. And as such it needs to be properly set. Also remember that this illusion is awesome because it works with 3 dimensions.
The reflection of the projection appears to be 'in' the room. Plan accordingly.
The rule of thumb here is that the distance from the image to the picture plain is the sam distance the viewer perceived daise to be in the room. If you look at my diagram, you can see how she appears to be standing in front of the desk. Use this to your advantage. For more advanced techniques you can implement props 'in front' of your ghost but remember you need to use custom footage at that point.that's another tutorial. For mine, I decided to set it as a sort of seance/wedding.
I used my office desk as an 'altar' and put the collected writings of Chaucer on it (the biggest and oldest book I have.) I placed candles, a skull, some dead flowers and so on. These are details. And while they will go largely unnoticed, if you have your backpack and a bottle of Sunny-D sitting out, people WILL notice.so be smart about your scene. Step 11: Protecting the Illusion. I noticed when I was outside, and you can see in the movie above, that the edge of the plexi was visible.
This is where the spiderwebs came in handy. Curtains would work too, but I needed to block the viewer from seeing the edge of the picture plain.
I also recommend closing off that room. During a dry run, I got it all set up and ordered a pizza. When the delivery guy showed I was all excited to hear how freaked out he was. I opened the door, he gave me my pie, told me the score of the World Series game and left. Why wasn't he amazed? Oh.maybe because the cats had gotten on the computer and now I was projecting a ghost screen saver.
Who would be terrified of bobbles floating around? Protect your haunt Step 12: Back Story. Sweet thank you.you clearly have put a ton of time into it. Your nursery sequence is inspiring. Literally.I am now planning on using my Pepper's setup for a haunted nursery.children at terrifying. Switch out my altar for a bed, throw in an antique rocking horse (that rocks itself of course) and a ghost of a child playing alone who suddenly looks up and says 'Are you my mommy' then jumps to the glass and says.' I want to play with you.forever' before turning into a demon.
This is definitely happening. (RE the Haunted Nursery).if you happen to do any of my ideas full scale, I would KILL to see video of the effects.:) 'children are terrifying' Oh, I agree. That's what basically inspired my Daark Orphanage idea.that, and a story I once read about the executives at Disney getting together in the 70's to discuss possible additions to the Haunted Mansion they were planning to add to Disney World.the discussion was about the Endless Staircases that were planned to be added in. One young, new guy chimed in with, 'Hey, a red ball bouncing slowly down the stairs, while accompanied with the sound of a child laughing would be CREEPY, eh?' Every exec in the room slowly turned to face the new kid.
Then the man at the head of the table cleared his throat, and stated. 'Disney doesn't do dead kids.' I recall reading that and thinking immediately to myself, 'Well, that's their loss.because dead kids are freaky scary and COOL!' .;) Oh, you might also dig this.I had the idea, 'what if there was a movie based on my dark ride attraction'? I think it might.I've never tried it before personally. If you are ok with a static image the only issue I could think of would be the fact that you would have to make a stencil of whatever you were trying to project as well as the image itself. This would have to lay over the image in order to block out any surrounding light from being projected.
Plug it in with a cord you've modified with a resistor: And then the overhead will flicker on and off randomly (I have not tried this technique and cannot recommend it, but there it is) As always, when working with electricity.be VERY careful. Good luck and please let me know how it goes!!!
Invisibility cloaks. Spider silk that is stronger than steel. Plastics made of sugar that dissolve in landfills.
Self-healing military vehicles. Smart pills and micro-robots that zap diseases. Clothes that monitor your mood. What will the future bring, and what will it be made of? In NOVA's four-hour series, 'Making Stuff,' popular technology columnist David Pogue takes viewers on a fun-filled tour of the material world we live in, and the one that may lie ahead. Get a behind-the-scenes look at scientific innovations ushering in a new generation of materials that are stronger, smaller, cleaner, and smarter than anything we've ever seen. 'Making Stuff' is produced in cooperation with the (MRS), an international organization of nearly 16,000 materials researchers from academia, industry, and government, and a recognized leader in promoting the advancement of interdisciplinary materials research to improve the quality of life.
What is the strongest material in the world? Is it steel, Kevlar, carbon nanotubes, or something entirely new?
NOVA kicks off the four-part series 'Making Stuff' with a quest for the world's strongest substances. Host David Pogue takes a look at what defines strength, examining everything from steel cables to mollusk shells to a toucan's beak.
Pogue travels from the deck of a U.S. Naval aircraft carrier to a demolition derby to the country's top research labs to check in with experts who are re-engineering what nature has given us to create the next generation of strong stuff. The other programs in the 'Making Stuff' series are 'Smaller,' 'Cleaner,' and 'Smarter.'
'Making Stuff' is produced in cooperation with the (MRS), an international organization of nearly 16,000 materials researchers from academia, industry, and government, and a recognized leader in promoting the advancement of interdisciplinary materials research to improve the quality of life. C Lewis Azad NanoTech Institute, UTD Jim Bales Edgerton Center, MIT Ray Baughman The University of Texas at Dallas Mark Eberhart Author, Why Things Break Joan Embery Embery Wildlife Conservation Nicholas Godley Fashion Designer Randy Lewis Molecular Biologist, UW Marcio Dias Lima NanoTech Institute, UTD Mark Meyers Materials Scientist, UCSD Tucker Norton Ballistics Scientist John Paules GM, Ellwood Technologies Scot Vannorman United States Navy Danny Womack Owner, Outlaw Motor Speedway Education and Outreach Resources. How small can we go?
Could we one day have robots taking 'fantastic voyages' in our bodies to kill rogue cells? The triumphs of tiny are seen all around us in the Information Age: transistors, microchips, laptops, cell phones. Now, David Pogue takes NOVA viewers to an even smaller world in 'Making Stuff: Smaller,' examining the latest in high-powered nano-circuits and micro-robots that may one day hold the key to saving lives. The other programs in the 'Making Stuff' series are ',' ',' and '.' 'Making Stuff' is produced in cooperation with the (MRS), an international organization of nearly 16,000 materials researchers from academia, industry, and government, and a recognized leader in promoting the advancement of interdisciplinary materials research to improve the quality of life.
Making Stuff: Smaller PBS Airdate: January 26, 2011 DAVID POGUE: Imagine a world with buildings that can ride out earthquakes; bacteria that make gasoline; tiny devices that can repair individual cells, or even D.N.A.; gossamer threads, strong enough to hold up a bridge; or an elevator to the stars. These visions of the future are based in the discoveries of today, as a new science of materials emerges from the elemental building blocks of the universe, promising a future in which we can create virtually anything we want, atom by atom. I'm David Pogue, and I'm on a quest to discover how the world's smallest materials are changing our lives: swarms of nano-machines that combat cancer on the cellular level with bee venom. Bee venom is a cancer drug? Samuel Wickline (Cardiologist, Washington University): Yeah, it's an excellent cancer drug. DAVID POGUE.computer chips, one-atom-thick and up to a thousand times faster than silicon chips today. Come on; now you're hurting my brain.
Mishkin (Gastroenterologist, Boston University): This capsule is acquiring images at a rate of two frames per second. DAVID POGUE.and high definition cameras, an inch long, monitoring our bodies from within. Oh man, I think I just banged the top of the eyeball.
How far can we go. That's a robot? Bradley Nelson (Institute of Robotics, ETH Zurich): That's a robot.
DAVID POGUE.in Making Stuff Smaller? Right now, on Nova. As tech columnist for the New York Times, I'm always on the hunt for the next killer gadget. Wow, so I can play my records straight into the iPhone?
Adam Cohen (Consumer Electronics Show participant): That's right. DAVID POGUE: That's very cool. Each year, my beat brings me to the Consumer Electronics Show, in Las Vegas, to investigate the latest trends in new tech. Summer Douglass (Consumer Electronics Show participant): It's a watch that is also a cellular phone, an Mp3 player, a camera, a video camera. DAVID POGUE: Somehow, the electronics world has found that the key to making stuff better is making it smaller. David Albers (Consumer Electronics Show participant): So, that's the new flagship L.E.D.
DAVID POGUE: Wow. Take the T.V. Ten years ago, the first flat screens cost as much as $12,000. They had thick glass panels and weighed a whopping 85 pounds, but now? DAVID ALBERS: This T.V. Is point-three inches deep. DAVID POGUE: Are you kidding?
So, the nice thing is when they FedEx it to you, they can just slip it under the door? DAVID ALBERS: Exactly. DAVID POGUE: I'm on a quest to discover why size matters, why getting smaller leads to such gigantic benefits. Amy Koppman (Consumer Electronics Show participant): Performance on it is phenomenal in the light.
You have an f2.8 lens, 24-millimeter wide. It's just a great piece. DAVID POGUE: It's crazy. If everything we own had improved over the last 25 years as much as electronics have, the average family car would travel four times faster than the space shuttle; houses would cost 200 bucks. What's the secret behind electronics stunning advances? How many times have I reviewed these and wondered exactly what's inside there?
Do you mind if I have a look? AMY KOPPMAN: No, not at all. DAVID POGUE: I'd like to have a look inside. AMY KOPPMAN: Yeah, please do.
DAVID POGUE: Where I come from, you want to know how something works, you cut it open. Sony versus saw; here we go.
You guys standing far enough back? Because I don't want anyone to get hurt.
What do you think we'll find? And now, let's see what really is on the inside of a digital camera.
Not much really, and no moving parts at all! This digital camera. AMY KOPPMAN: This is the brains.
DAVID POGUE.runs on a half-inch-wide microchip. So it seems like this is really the heart of the camera.
A lot of it just exists so that I can handle it with my big human hands. AMY KOPPMAN: Correct, 'cause that's not exactly the most comfortable form factor you want to be using right there.
DAVID POGUE: I know. Honey, smile. Come on, let me see you smile. This tiny wafer contains a highly sophisticated machine. What's it made of? A computer chip is like a densely packed city: a solid slab of silicon, sprinkled with other elements like boron and arsenic, topped by layers of metals and ceramics.
They are laid out like tiny functional neighborhoods. Over here is memory. Fifty years ago, you'd have needed a whole building full of vacuum tubes to store just a fraction of what fits in here. Over here is where data comes in and out of the chip. Fifty years ago, the fastest computer on Earth could process, maybe, a few hundred punch cards a minute.
Today, data goes in and out billions of times faster. And here is the processor. Fifty years ago, a computer could add a few thousand of numbers in a second.
In the same amount of time, this tiny chip can perform billions of calculations. Scientists have discovered that the secret to cheap computing power is size. When we find the right materials, and make them small, they change the world. The race to miniaturize began 500 years ago, with an invention that, in its day, was the first personal computer. I'm talking about the watch. How did they go from big wall-mounted grandfather clocks to something you could wear on your wrist?
Pierre Gygax (Chief Operating Officer, Ulysse Nardin): The miniaturization, more functions in a smaller space. DAVID POGUE: Pierre Gygax is a watchmaker, in Switzerland.
Some of his watches have more than 400 components. And how small are some of the parts? PIERRE GYGAX: There are parts, which are point-zero-zero-six millimeters.
So that means a half the thickness of a hair. DAVID POGUE: Wow.
Hundreds of precision metal pieces all driven by a simple mechanism that all clocks have in one form or another: the oscillator, the beating heart of the machine. It's the piece that puts the tick and the tock in time. PIERRE GYGAX: You know the time is flowing. And it's always difficult to measure something flowing. So, what we do is we, we cut the time in slices.
And the oscillator is counting the slices. DAVID POGUE: The original oscillator was the pendulum, slicing like a knife through time, with each swing counted by the movement of circular gears.
But pendulum clocks work only if they are upright in a fixed position. So, in the Middle Ages, clocks were confined to immovable structures like towers or furniture. But in the 15 th century, the invention of the mainspring changed everything. It was essentially the first battery, a metal coil that could store mechanical energy.
As it unwound, the mainspring powered a compact wheel. It was a major breakthrough. Suddenly, gravity and the pendulum were no longer necessary.
The new spring-driven mechanism made it possible to shrink the clock to fit into a hand or a pocket, and the pocket watch was born. PIERRE GYGAX: This watch is absolutely amazing. It shows the exact position of the sun and the moon, all around the earth, from the top of the North Pole. DAVID POGUE: Oh, man, that's really cool.
And how much does this watch go for? PIERRE GYGAX: Between $80- and $90,000. DAVID POGUE: But no need to spend 90 grand to find out what time it is. Nowadays, super accurate watches are disposable, thanks to another great clock revolution, which began in the 1960s. Out went the spring and mechanical oscillator, replaced by a tiny sliver of solid mineral quartz. Slice a piece of quartz small enough, send an electric current through it, and it vibrates fast. A quartz-driven clock can accurately chop time into millionths of a second, but the biggest selling point for quartz is that it's cheap.
That's because quartz is actually silicon, commonplace sand, the second most abundant element on Earth. For the first time, a material replaced a machine, opening the door to a new era of miniaturization. But silicon can do more than just mark time.
It's a member of a strange class of elements called semiconductors, found on the table of the elements. As the name implies, they occupy a middle zone between metals, which conduct electric current, and insulators, like rubber and plastic, which don't. Think of water flowing through a pipe, an insulator is like a pipe that's frozen: electrons can't get through.
Semiconductors are materials that change from free-flowing conductor to a frozen insulator and back again, simply by zapping them with an electric current. Switches made out of semiconductors are called transistors, and their amazing on-again, off-again switching ability made the computer revolution possible.
But how did they get to be so small? One great place to look for answers is Intel, a pioneer in squeezing tiny transistors onto computer chips. I've met a lot of scientists who talk about switches and semiconductors, and somehow they are fulfilling the same function, but, but what is it? Smith (Vice President, Intel Corporation): What we're trying to build with a semiconductor is a switch. This is one from the, the wall, something you'd use to turn on a light and turn off. And, in fact, when we push the switch up, we give an input and the light is an output.
DAVID POGUE: So, in science fair terms, a switch then, lets electricity go through or stops it. Stephen Smith: Exactly. Based on the input, we change the flow of electricity.
DAVID POGUE: Electricity on or off. It's the only language computers understand. When the switch is off, the computer reads a zero. When the switch is on, the computer reads a one. String a bunch of switches together and you can create a code. With just eight switches, you can represent any symbol on a keyboard. For a page, you need about 25,000 switches.
One-point-four million will get you a second of music. Photos need tens of millions. We're talking about tens of billions. The more switches, the more power. The story of the computer revolution is the story of the shrinking switch. Early computers used mechanical relays and vacuum tubes as switches. Building a machine with just a few thousand took up rooms of space.
But the silicon transistor changed all that. Because it's a material, not a machine, it's easy to shrink. STEPHEN SMITH: The exciting part about silicon transistors is we're actually using the atomic properties of the silicon. So rather than actually having to craft something, to build a switch, to build the pieces, to build a spring, I actually, by doing some smart engineering, can get the electrons to flow by using the properties of the atom.
And we brought some material to illustrate that. What we have here. DAVID POGUE: We happen to have a hunk of cheese lying around the lab? STEPHEN SMITH: A hunk of cheese, a hunk of cheese. So think of this as the silicon material. I can actually take a slice of that silicon, and I can use the atomic properties of this slice to build those transistors.
DAVID POGUE: Ladies and gentlemen, the Pentium-cheesium-five. Um, I understand that it works really well with the computer mouse. (You can use that.) All right, so you're saying that one beauty of silicon is that you can cut it in half and it's still silicon? STEPHEN SMITH: Exactly. DAVID POGUE: And you can slice it again, smaller and smaller and smaller, but it still does just as good a job at passing along the ones and zeros.
STEPHEN SMITH: Absolutely. And I can use those material properties until I get down to the size of only a few atoms of silicon. DAVID POGUE: Wow.
Which is not something you could do to make mechanical switches smaller, right? Like, if I wanted to make this smaller, you know, I can't just go like this.
STEPHEN SMITH: Wow! DAVID POGUE: And you can have a smaller one. Clearly, this is not going to be a smaller, good switch. STEPHEN SMITH: Right. Uh, but this is silicon. It is a purified element that one mines. DAVID POGUE: All right, so what does it look like in the computer, then?
STEPHEN SMITH: Well, by the time it gets to the computer, it actually is one of these devices. So, this shiny surface is a piece of refined silicon. It has transistors built into it. We've actually flipped it over so that the transistors are on the other side, and what you see is the back of that piece of silicon. DAVID POGUE: And this is how many of those little on-off switches? STEPHEN SMITH: This is almost a billion transistors.
DAVID POGUE: Wow. A billion switches on a one-inch chip. What's even more astonishing is that one of the founders of Intel saw this coming. In the '60s, Gordon Moore predicted that the size of transistors would shrink by half every two years, each time, doubling the number that could be squeezed onto a single chip. This idea is known as Moore's Law, and it has proved to be incredibly accurate.
But now, 50 years later, Moore's Law may finally be running out of steam. The transistors that power our stuff are about as small as they can get, unless scientists can come up with a new way of packing them ever-more tightly together. To see one of those possible solutions, I've crossed the country to visit the IBM Research and Development.' So this is Moore's Law of Italian cooking? Frances Ross (IBM Research Division): That's right. What we're going to do is explain why it's so important to get the transistors smaller and smaller.
DAVID POGUE: Frances has a pretty appetizing way of visualizing this law and its limitations. Like pepperoni slices, the transistors on a silicon chip are flat. Okay, so here's our. Frances Ross: Silicon wafer. DAVID POGUE.silicon wafer.
Frances Ross: Now, these are the old-fashioned transistors. They're much larger, and you can see that you can't put that many onto each wafer. DAVID POGUE: So this would be a 1960 iPod? Frances Ross: I think so, yes. This would be a '60s type of thing.
So, let's take off these old transistors and replace them with some new transistors. DAVID POGUE: Oh, these are much smaller! Frances Ross: Yes, these new transistors are much smaller. DAVID POGUE: Technology has marched on. Frances Ross: That's right. It's Moore's Law, in action. DAVID POGUE: So, in other words, all we have to do is make the transistors smaller every year, forever, and our gadgets will always be more powerful and more compact.
Frances Ross: That would be wonderful, but we can't make our pepperoni slices much smaller than this. And these transistors are now packed together about as close as we can get them. DAVID POGUE: The pizza party can't go on forever. There's a limit to how small you can shrink the transistors. If you reduce the surface area of a transistor too much and place it too close to its neighbor, electricity starts to leak, causing a short circuit. Frances Ross: We've run out of area, so there's only one way to go, and that's upwards. DAVID POGUE: Slim Jims?
Frances Ross: That's right. This is a vertical transistor. Instead of having flatter, smaller transistors we go in the other direction. DAVID POGUE: Excuse me, vertical transistors? Frances Ross: Vertical transistors.
DAVID POGUE: With little toothpicks on the bottom? Frances Ross: That's just for demonstration purposes. DAVID POGUE: Oh, okay.
By building vertical transistors, called nanowires, Frances can increase surface area, without bringing the transistors closer together, so no short circuit. So this is what you're doing at IBM? You are making these? FRANCES ROSS: That's right. They're called nanowires, and the real thing is about a million times smaller than this. DAVID POGUE: A million times smaller?
FRANCES ROSS: That's right. DAVID POGUE: Well, that would be hard to see! They're hard to see. But this is not a nanowire.
This is a silicon sliver Francis uses as a surface to grow them. FRANCES ROSS: We get tens of millions of wires on each of these specimens.
DAVID POGUE: Come on! FRANCES ROSS: Yes.
DAVID POGUE: Now you're hurting my brain. FRANCES ROSS: Oh. DAVID POGUE: She carefully loads the wafer into a molybdenum clip and slides it into a custom-built oven, where she'll bake it at 1,100 degrees Fahrenheit. You know, I was just thinking, Frances.
I don't think you have enough aluminum foil on this oven. FRANCES ROSS: Yes, it's the question that everyone asks. It holds the heat better. DAVID POGUE: Aluminum foil?
FRANCES ROSS: That's what, that's what we use. DAVID POGUE: Isn't that a little low tech?
FRANCES ROSS: That's right; whatever works. DAVID POGUE: Oh, my gosh. So those little spires.? FRANCES ROSS: Those are the nanowires. DAVID POGUE: So, you bake those up? FRANCES ROSS: Just grew these, yes.
DAVID POGUE: We can see them, because this oven doubles as an electron microscope. All right, so these are them, huh? FRANCES ROSS: This is 30,000 times magnified.
DAVID POGUE: Thirty-thousand times? FRANCES ROSS: That's right. So here's the column of silicon that's the nanowire, and here's the gold droplet, on the end, that actually makes it grow. DAVID POGUE: It's weird.
It looks like matchsticks or weird mushrooms. FRANCES ROSS: They do.mushrooms, that's right. They look to me like mushrooms. DAVID POGUE: That's amazing. FRANCES ROSS: So we're trying different catalysts, different recipes, but this here is the future of transistors DAVID POGUE: Wow. While scientists like Frances try to find ways to push silicon to its limit, others are pinning their hopes on a new material that lets electrons flow a thousand times faster than they can in silicon. And it's called 'graphene.'
Pablo Jarillo-Herrero (Physicist, Massachusetts Institute of Technology): When graphene happened, I just couldn't stop myself from going into it. It was so beautiful, I just couldn't stop.
I immediately jumped onto it. DAVID POGUE: This is Dr. Pablo Jarillo-Herrero, a professor at M.I.T. And graphene guru. PABLO JARILLO-HERRERO: So, here I have graphene.
Graphene is the thinnest material that exists. This is just one-atom-thick, okay, sheet of graphene and you can see that it is perfectly visible. So, it's part of the magic of graphene.
You can just see it, even with your eyes. DAVID POGUE: You heard that right. This grey square of graphene is just a single atom thick.
Although graphene was discovered only recently, it's been hiding in plain sight for ages, in a material you probably have on your desk: graphite, also known as pencil lead. PABLO JARILLO-HERRERO: You can write with a pencil because graphite is a layered material. And as you write, you are leaving traces of these layers on your piece of paper. So graphene is really just one sheet of this graphite material, a one-atom-thick sheet. DAVID POGUE: That makes graphene an ideal conductor. At only one atom thick, there's nothing to restrict free electrons, which flow across the surface of the material, like water across flat ice. PABLO JARILLO-HERRERO: Graphene is a very special conductor.is the best conductor, and we're now studying those properties and learning how fantastic this material is.
DAVID POGUE: And scientists have also figured out how to make transistors out of graphene, giving it the ability to speak the language that electronics and computers understand. PABLO JARILLO-HERRERO: So, I'm excited. It's beautiful.
Here you have a material that will enable high-speed, ultra-high-speed electronics at very low power. DAVID POGUE: But it gets even better. Turns out, the only tool you need to make graphene is a piece of tape. PABLO JARILLO-HERRERO: It is so simple, any high school student can indeed make one atom-thick devices with this.
It's really amazing. That scotch tape is going to be folded into two, and then, when we separate that tape, this graphite naturally exfoliates in two pieces. Then we're going to fold it again. It will split into four pieces. Do it again and again, making the piece of graphite thinner and thinner and thinner. Basically until we cover the entire tape with graphite.
We're then going to take a silicon chip, deposit it on top of the tape. And what we're hoping is that the graphite pieces which are on the tape are going to get in intimate contact with the silicon. So when you remove the chip and you look then with an optical microscope, you can see the one-atom-thick material.
And that's graphene. DAVID POGUE: Graphene promises to make the impossible possible, letting electrons move across its surface at virtually the speed of light and generating almost no heat.
In fact, graphene is such a revolutionary material that in 2010, a mere six years after its discovery, the two Russian scientists who first made it received the Nobel Prize in Physics. The computer chips of tomorrow could be a quantum leap forward: computers with nearly limitless processing power; every book ever written, stored on a tiny chip; a highway system so smart it could control millions of cars without a single accident. And it's not just about our gadgets, it's about us. While the electronics story continues to unfold in amazing ways, the story is beginning all over again with a materials revolution in medicine.
It's not a new idea. Remember this?
Audio Clip ( Fantastic Voyage, Film Clip) Phase One calls for miniaturizing a submarine and injecting it into the carotid artery. DAVID POGUE: Fantastic Voyage, it was the sci-fi smash of 1966. Audio Clip ( Fantastic Voyage): Phase One, Phase One. DAVID POGUE: Scientists shrink a team of doctors and send them into a sick man's body, on a mission to cure him. Audio Clip ( Fantastic Voyage): Stand by for injection. All stations stand. Tracking post.
DAVID POGUE: Today, as our devices get smaller and smaller, Fantastic Voyage is beginning to look like prophecy, the kind of thing that can change lives. DANIEL MISHKIN: Hi, Courtney. Courtney DeSisto (Patient): Hi, Dr. DANIEL MISHKIN: Good and yourself?
COURTNEY DESISTO: I am good. DAVID POGUE: Today, Courtney will be taking a pill, but it's not just any pill. It's a miniaturized camera. DANIEL MISHKIN: This capsule is a miniaturized camera. Every time it blinks it's actually taking a picture.
It's acquiring images at a rate of two-frames per second. COURTNEY DESISTO: Okay. DANIEL MISHKIN: And what I'm going to get you to do is actually to swallow the capsule.
COURTNEY DESISTO: Okay. DANIEL MISHKIN: And as the capsule goes through the G.I.
Tract it's going to be taking pictures of what's going on inside. COURTNEY DESISTO: Wow. DAVID POGUE: It's called the PillCam, and it travels through the body just like a piece of food, taking 55,000 pictures, over the course of eight hours. DANIEL MISHKIN: Why don't we actually put it inside your hand?
DAVID POGUE: Pictures that can provide a diagnosis that once would have required surgery. DANIEL MISHKIN: All right, so as you move it around, we can actually see the folds of your hands, with excellent magnification. So once we actually go ahead and ingest the capsule, it's going to give us that same magnification of what's going on inside. COURTNEY DESISTO: Wow, that's really cool.
DANIEL MISHKIN: It actually has a wireless transmitter, that's going to transmit the images to the data recorder that you'll be wearing over the course of the day, and I'm going to download the images and be able to look at them and analyze exactly what's going on. COURTNEY DESISTO: Okay. DAVID POGUE: The PillCam is made of an inert plastic that doesn't create a toxic response in the body. Inside, is a mini-catalog of the electronics industry: a tiny video camera and flash, a radio transmitter, a battery, and, of course, a computer chip to drive it all.
Twenty-five years ago, all of those components would have taken up a cubic yard of space. Today, it all fits inside a one-inch capsule that weighs only a fraction of an ounce. DANIEL MISHKIN: So let's go ahead and ingest it. COURTNEY DESISTO: Okay. DANIEL MISHKIN: Ready? Into your mouth. I'll give you a glass of water.
Now I see your teeth. And, go ahead, down the hatch. So that's it. That's the hardest part. COURTNEY DESISTO: Okay. DANIEL MISHKIN: Just remember, over the next two hours, do not drink anything.
COURTNEY DESISTO: Okay. DAVID POGUE: As the PillCam moves through Courtney's digestive tract, it records what it sees, eventually giving Dr. Mishkin a front-row seat as he looks for abnormalities. DANIEL MISHKIN: Right now, we're looking at the small intestine. It's able to see 360 degrees, such that it's like looking down a gun barrel.
The capsule is great at acquiring images, but I'm hoping that as the next generations of the, this capsule develop that it's not only be able to take pictures, but it will eventually be able to biopsy—sample the tissue in that area—or even deliver a treatment, such as placing a clip on a bleeding site, or even deliver medications. DAVID POGUE: The PillCam is the pocket watch of today, a super-miniaturized machine that liberates the patient. It took centuries to make the leap from mechanical watches to computers, but in the world of microscopic medicine, the story of smaller is unfolding on a vastly accelerated timeframe. In fact, scientists are on the verge of realizing a 21 st century version of the Fantastic Voyage story. They are developing microscopically small robots that travel into the body's deepest reaches to diagnose, treat, and even destroy deadly illnesses. This is your lab? BRAD NELSON: This is my lab.
DAVID POGUE: This is where you build your robots? BRAD NELSON: This is where we build the robots. DAVID POGUE: This is Brad Nelson. He's created a robot that could help cure blindness. Oh, nice, it's incredibly lifelike. BRAD NELSON: Yeah, that's a mannequin. DAVID POGUE: Oh, sorry.
BRAD NELSON: These are the ones we build. DAVID POGUE: What? That's a robot? BRAD NELSON: That's a robot. DAVID POGUE: Looks like a splinter. BRAD NELSON: Well, this is a microrobot.
We use them to help perform surgeries on the eye or inside of the eye. DAVID POGUE: The device is only a hundredth of an inch wide, small enough to fit into the needle of a syringe, like the tiny sub in Fantastic Voyage. But the similarity ends there. This unmanned device is designed to treat a type of blindness caused by blocked blood vessels in the retina, the tissue where images are formed. The robot delivers an extremely small dose of medicine to restore blood flow and vision. That makes me think that this little tiny thing has batteries and little propellers and some kind of knowledge to know where to go in the eye.
I have a hard time believing that. BRAD NELSON: That's right. The way we energize is we use externally generated electromagnetic fields. So, basically, it's a magnet. DAVID POGUE: To make the device small enough, Brad had to abandon the idea that robots have to be mechanical.
Instead, he focused on finding a material that would let him eliminate bulky moving parts. He chose two elements, samarium and cobalt. Combined, they form a material highly sensitive to magnetic fields, which means that Brad can direct the movement of the robot without touching it. Once again, a material replaces a machine and the device gets smaller. BRAD NELSON: So then, besides just the robot, what we also have is this system here, of electromagnets, and so what each of these copper coils do, is they generate magnetic fields. DAVID POGUE: Oh, man.
Yeah, you got a bunch of them in every direction. BRAD NELSON: So we have eight of these here. That's why we call this the OctoMag. DAVID POGUE: OctoMag? BRAD NELSON: That's right. DAVID POGUE: The OctoMag.
By adjusting the strength of these eight electromagnets, the surgeon can move the microrobot any direction along the x, y and z-axes, pushing or pulling it through the eye. But landing it on the tiny section of retina used for seeing in sharp detail takes lots of practice. And you've been practicing with dummy eyeballs, so far? BRAD NELSON: We use that, but we also use animal eyes as well. We get pigs eyes from our local butcher.
DAVID POGUE: You buy eyeballs from the butcher, from cadavers? BRAD NELSON: That's right, Christos, one of my PH.D. Students.Christos goes in the morning, early in the morning, to the butcher and asks for eyeballs.
DAVID POGUE: Christos. Christos Bergeles (Student, Institute of Robotics, ETH Zurich): Fine. DAVID POGUE: Oh, my.
These are the pig eyes? Torrent Kevin Hill Saison 12 more. Christos Bergeles: Exactly.
Twenty pig eyes fresh from the butcher, ready to be prepared for experiments. DAVID POGUE: You must be a big hit around Halloween. And what about this guy, what's this all about?
Christos Bergeles: Ah, we call him Mr. DAVID POGUE: Mr. Christos Bergeles: Well, you have to give them a name. Then we put the eyes in this hole here.
DAVID POGUE: Once the eyeball is secured inside the socket, we insert a light probe. Christos Bergeles: That's the light there. DAVID POGUE: Oh, okay. I can actually see the light in there, very cool.
This tiny L.E.D. Lets us see what we're doing when we drive the robot. So, this is the robot right here? Christos Bergeles: Mm hmm. DAVID POGUE: Okay. And this isn't fake? We're really seeing this live from the microscope, right now, right?
Christos Bergeles: Yes. You can move this guy around. DAVID POGUE: Okay. Sure enough, I push right, he goes right; left, he goes left.
Let's see when I go down over here. Christos Bergeles: And then you can pull up and you can see it. DAVID POGUE: Oh, it's getting bigger.
Christos Bergeles: Exactly. This means that it's moving higher, away from the retina. DAVID POGUE: Closer to the surface of, oh man!
I think I just banged the top of the cornea or whatever you call it. Christos Bergeles: Exactly. So that's the very top, and this is where the liquid ends. So you see this, this effect. DAVID POGUE: Now let me push down.
Christos Bergeles: When you push down, it starts slowly going into the retina. DAVID POGUE: It's sinking, sinking! Wow, that's really cool. Christos Bergeles: So, now you've reached the bottom; you're touching the retina.
DAVID POGUE: Yeah, it's quite responsive. I can go right up here. Eventually, Brad hopes that there will be a commercial version of his device installed in doctors' offices. The magnets will be arranged in a housing that surrounds the patient's head while the doctor peers through a microscope to guide the drug-filled robot. Brad's initial success combining materials and magnetic fields to make tiny devices has encouraged him to be even more ambitious. His goal is to build a robot that can swim through blood vessels. But, along the way, he's discovered that the smaller you go, the stranger the world becomes.
Oh, dear, looks like the grad students have left their things out again. And the harder it is to get around. BRAD NELSON: So what we've seen, so far, are the microrobots for the eye. We're interested in going even smaller and trying to make smaller robots. So I set up an experiment here to, kind of, show you what some of the problems are when we try to make small things swim, and why it's so different from how big things, like fish or the toys like this, swim in water. DAVID POGUE: Okay.
BRAD NELSON: So what we've got here are two tanks. One is just regular water, out of the tap. This other one is glycerin. It's much thicker, like oil or corn syrup, something thick like that.
So let's look at how something like this toy goldfish is going to swim in water. DAVID POGUE: Wind her up? BRAD NELSON: Wind her up. There you go. DAVID POGUE: Okay, the tail goes back and forth. BRAD NELSON: Just the way you expect.
DAVID POGUE: I'd say that swimming is fairly effective. BRAD NELSON: Okay, he's got a twin over there. Let's see how he does in the glycerin. DAVID POGUE: And this one is going to go in the goop.
He wags his tail and doesn't move at all. BRAD NELSON: This helps us illustrate how water feels when you get small.
If you made yourself 10,000 times smaller and you jumped in this pool of water, it would actually feel more like you were swimming in glycerin here, or goopy stuff, like honey, or something thick like that. DAVID POGUE: Right. A swimmer the size of a bacterium would never be able to get around using flippers or the breaststroke, because, at that size, the friction from the water molecules becomes a major drag.
For a long time, scientists couldn't fig.